
Circular processes
Waste management
DAF is continuously working to reduce the amount of packaging material that arrives with parts at the production facilities. In a ‘war on waste’ awareness campaign, the company’s procurement team, and factory workers are encouraged to engage with suppliers to cut down on—or even refuse to accept—unnecessary packaging. For that reason, the focus is on reusable packaging. Components are loaded into a tailored DAF-designed return packaging at the supplier’s premises.
For years, DAF has a policy of zero waste to landfill. Waste that cannot be recycled is incinerated to generate electricity. DAF has reduced residual waste from the office buildings by 75% over the past 2 years, thanks to the EcoSmart program launched in 2022. After the success of the pilot project, even more waste separation units are installed in 2024 and employees are now using re-usable coffee cups to reduce the amount of unsorted waste.
At our production sites, we have our own recycling stations that collect over 100 different types of materials from concrete and cardboard to plastics, wood and metal. Different waste collectors and treatment partners process and sell these materials for reuse or recycling.
In 2024 several improvements have been implemented to further reduce disposable waste:
- Process improvements in the engine plant have improved metal chip separation from coolant, which can now be retained and reused;
- Waste streams of water-oil mixtures were selected to be cleaned at the DAF site instead of sending them to an external company for treatment, reducing over 80 tons of chemical waste annually;
- A paperless system was introduced for the transports of axles and cabs from our facility in Belgium to the Netherlands. The electronic CMR (e-CMR) system allows (forklift) drivers to complete consignment notes digitally on their onboard computers, streamlining the process and reducing unnecessary movements. This innovation enhances safety and eliminates printing costs and paper usage. In the coming years e-CMRs will be expanded to more inbound and outbound transports;
- The Cab factory targeted the use of cardboard and single-use wooden materials used for packaging and protection during transportation. By changing the previous packaging of wiper mechanisms, corner wings and fenders to returnable packaging, a reduction of 5 kg single-used packaging material per produced cab has been realized, this has saved over 250 ton of cardboard in 2024;
- At DAF’s water treatment facility in Belgium, the aeration system was replaced by a more efficient solution, reducing energy consumption by more than 50%. Through cleaning and redesigning the basin, as well as installing new blowers, water treatment efficiency was improved, and energy use lowered.
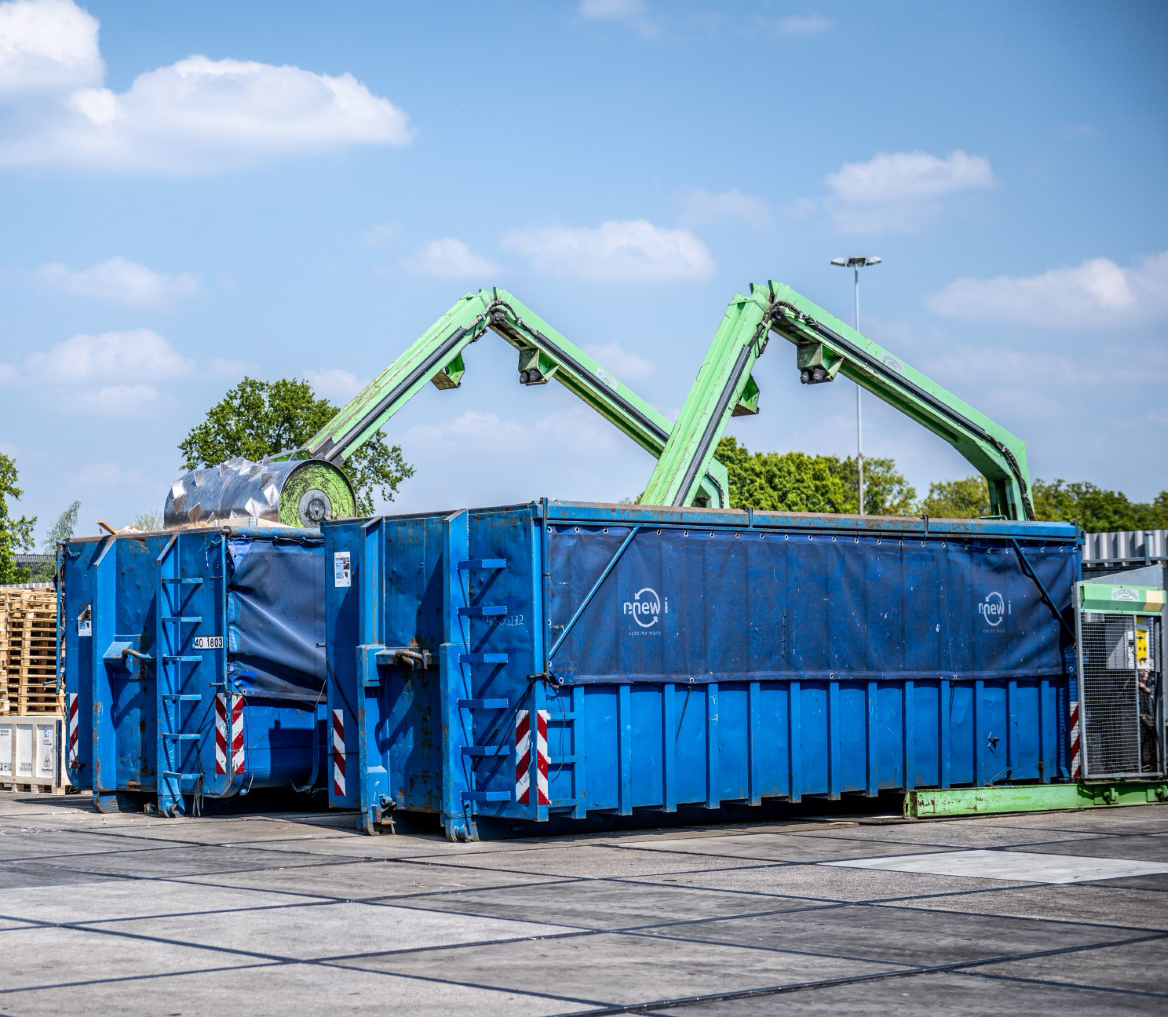
PACCAR Parts continues its packaging roadmap
During the development of new packaging to send spare parts to dealers, the key focus is always on sustainable solutions. Can we use less material, can we use recycled materials, is the material used easy to recycle? PACCAR PARTS also pays full attention to improving the existing range of packaging. In 2024, multiple packaging improvements were implemented:
- For several products a switch was made from wood to cardboard. Lighter packaging requires less energy and resources to produce and transport. Smaller packaging minimizes waste and optimizes space during shipping.
- All the European PDCs now use 100% recycled filling paper. This improvement resulted in a drop of virgin paper used within PACCAR Parts Europe from 21% to 7% of the total paper weight.
- A new design of the front window packaging allowed to create a sustainable solution fully made of cardboard, enabling easier and more adequate recycling.
- An initiative was started to collect pallets in the inbound area, and repurpose them in the outbound area, reducing waste volumes and the unnecessary purchasing of outbound pallets. In 2024, more than 10,000 pallets were reused, instead of disposed.
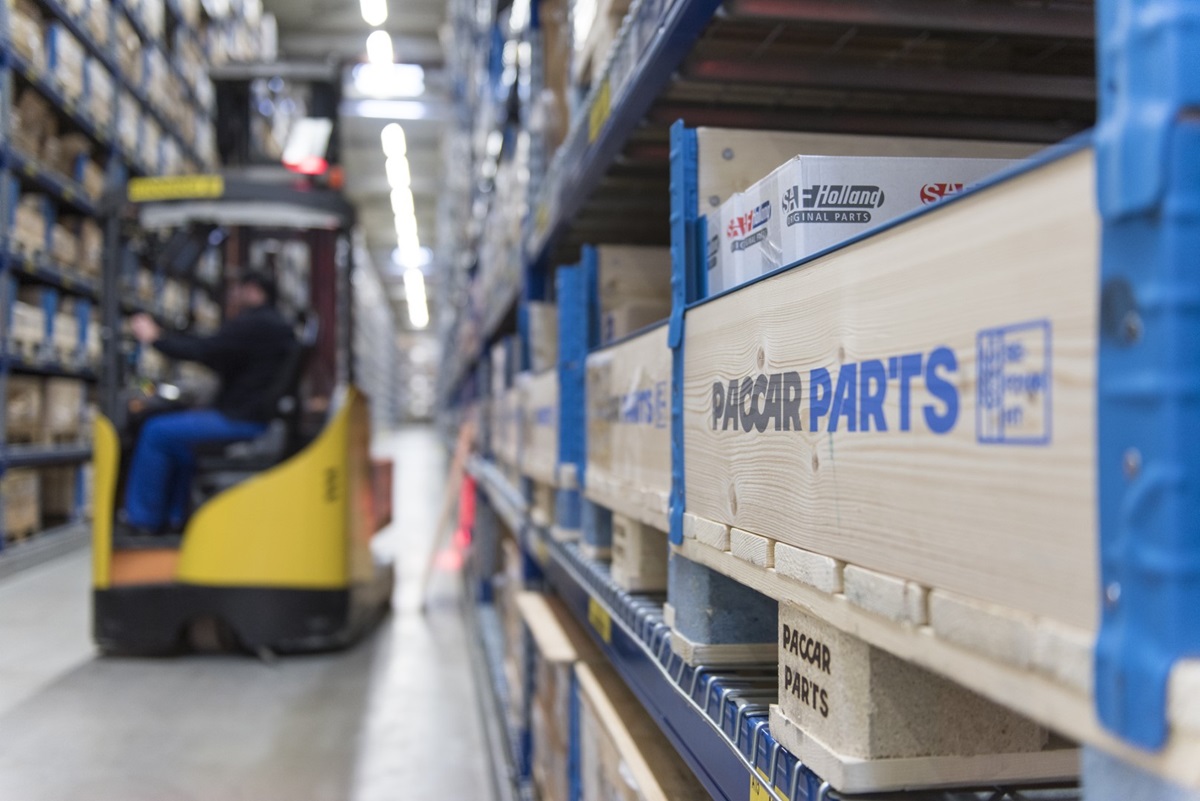
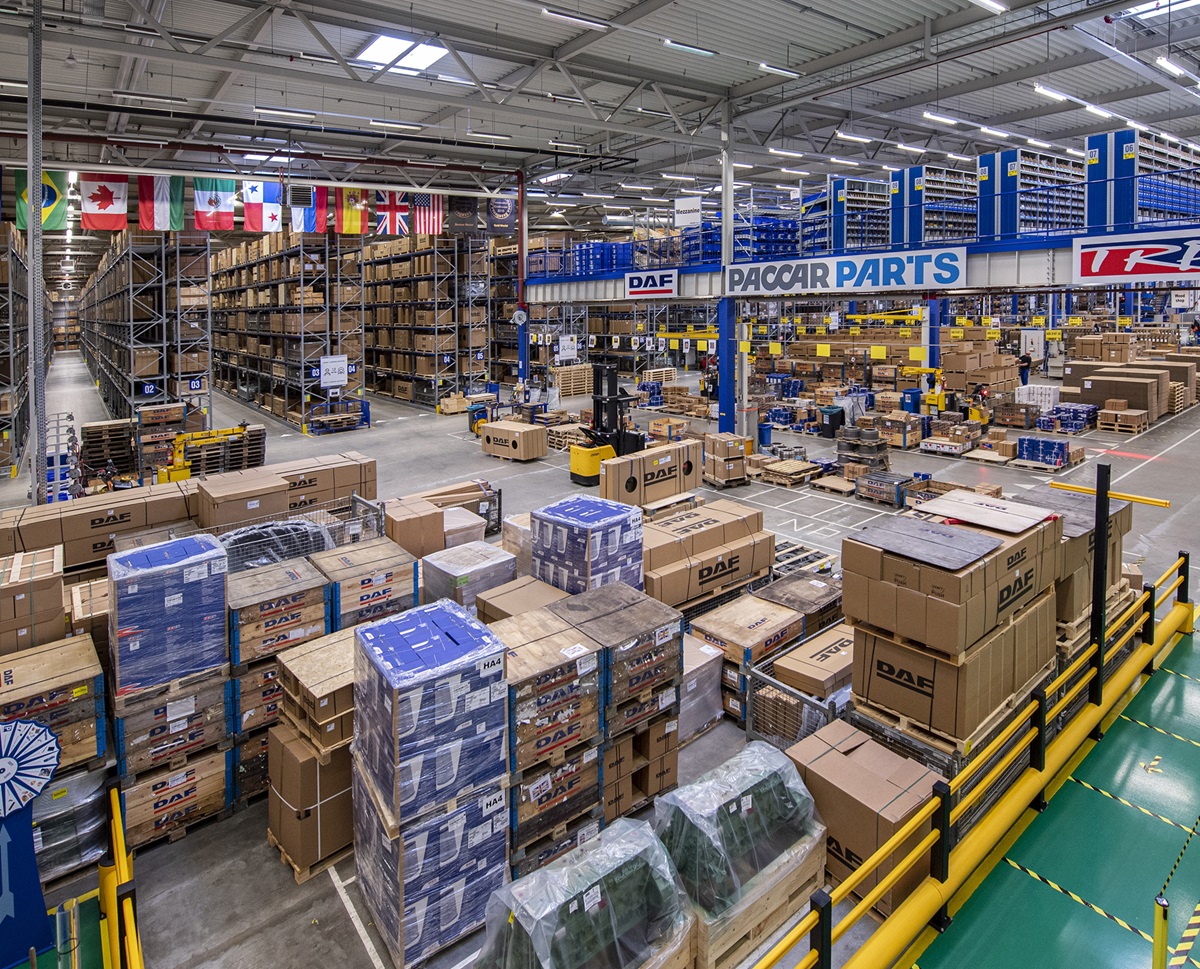
Related information
Go back to...